Push For Supply Chain Resilience, Reshoring Likely To Boost Industrial CRE
The coronavirus pandemic has left hundreds of U.S. manufacturers examining how to bring at least some of their operations and real estate footprints home.
Nearly two-thirds of North American manufacturers say they are likely to bring production and sourcing back to the continent, a new survey by industrial data and tech company Thomas shows. The company surveyed over 1,000 of the continent's manufacturing and industrial suppliers, with the help of business-to-business data gathered on Thomasnet.com.
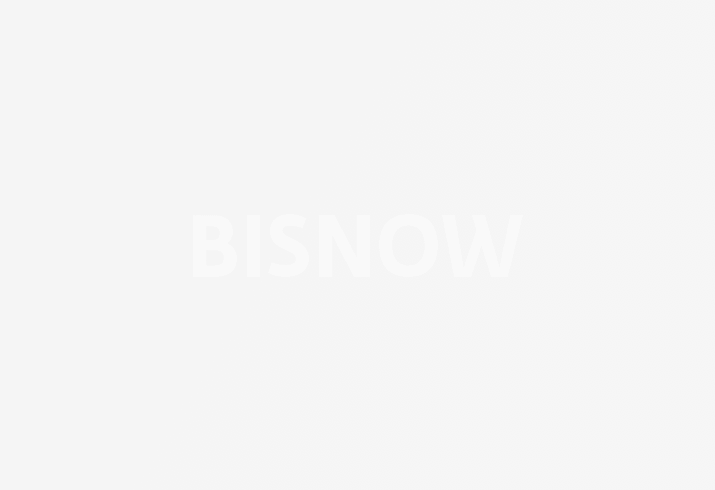
The U.S. manufacturing sector had seen a minor return stateside in recent years, with big domestic companies like Wal-Mart and Brooks Brothers bringing some operations back to the U.S., or "reshoring."
But since March, the share of North American manufacturers who say they are interested in bringing their operations home has leapt 10% to 64%, Thomas found.
"It’s been happening for the better part of a decade, and it’s been happening for a lot of reasons," Thomasnet.com President and CEO Tony Uphoff said. “It’s very clear COVID-19 is accelerating the hell out of that.”
Some companies had already been disappointed by high shipping and logistics costs associated with offshoring. As of late, that concern has been compounded in companies with supply chains starting in China, Uphoff said.
“We’re seeing the wholesale re-evaluation of supply chains taking place all across the platform right now," he said. "Every company is using this as a bit of a wake-up call.”
Colliers International Senior Vice President Gregory Healy, an expert in location strategy and supply chains, said a push for supply chain resilience will lead to an additional 750M SF to 1B SF of industrial space in the U.S. alone, as companies look to foster safety stocks of inventory in the already growing U.S. industrial CRE sector.
“No one wants to get caught in this situation again, where their supply chains are broken because they’ve been too reliant on one supplier or one region or one country for their goods," he said.
Companies also don't want to abandon the still-growing economies and middle classes of China and other Asian countries, Healy said, adding that they will likely pursue what he refers to as a "China-plus-one model."
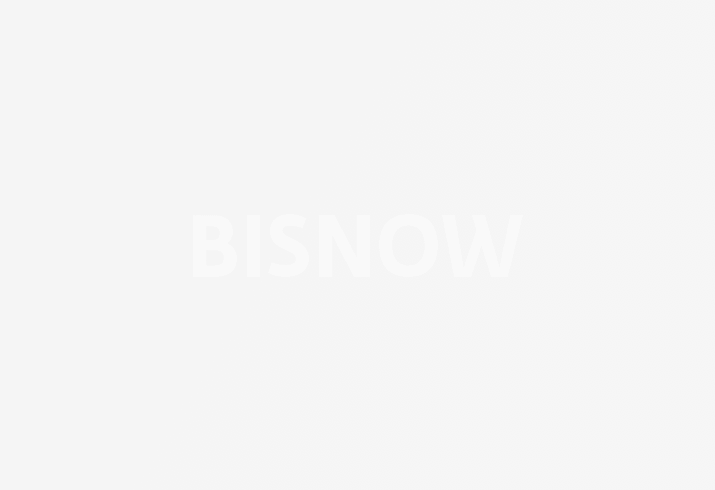
Existing manufacturing hubs like Pennsylvania, Wisconsin and Texas were named as the most likely reshoring destinations, Thomasnet data showed. Uphoff said the company also sees Mexico as an increasingly preferable option for North American companies still looking to manufacture outside the U.S.
Healy said Mexico will also probably see a bigger boost in manufacturing than any one state in the U.S. But he pointed to the southeastern U.S. and states bordering Mexico as positioned to see manufacturers boost demand for industrial CRE.
Industries most likely to see accelerated reshoring include transportation and construction, Uphoff said and automation might encourage reshoring while making it much easier.
Of the Thomas survey's 1,000-plus respondents, which have revenues ranging from less than $4.9M to over $50M, about 25% are considering expanding industrial automation as a result of the pandemic. An additional 20% already had such systems in place.
As automation technology has advanced, the economics of reshoring have been attractive, according to Uphoff. Boosts in productivity per SF have also allowed some manufacturers to avoid many shipping and logistics costs, by finding smaller facilities closer to customers.
"We can actually now stand up a relatively small-footprint manufacturing facility that’s unbelievably efficient, which means we can actually isolate a manufacturing facility near clusters of customers," he said. "You're literally in the backyard of the customer."