How Prefabrication And Streamlined Delivery Allow A 10-Story Parking Structure To Rise Quickly On A Crowded Site
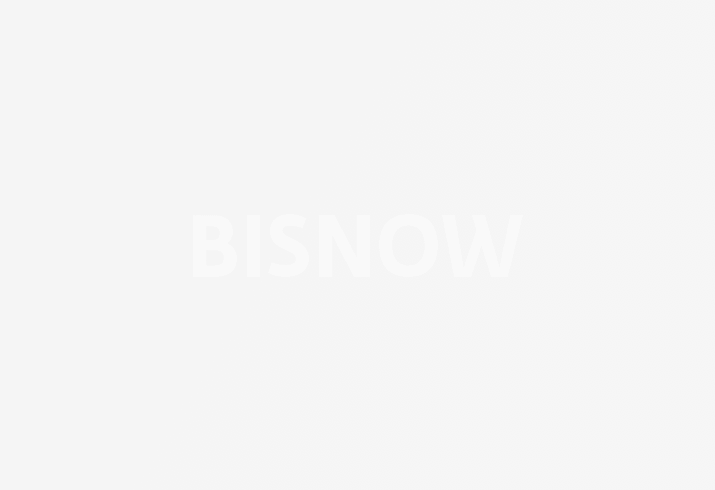
Kilroy Realty had multiple options to choose from for the design and construction of its new 10-story, 665K SF parking structure in Oyster Point in South San Francisco, California.
But in the end, the tight job site hugging San Francisco Bay, coupled with the need for the structure to be operational by summer 2024, made prefabrication the obvious choice for Kilroy.
“A traditional cast-in-place approach with a ton of workers on the site probably wouldn't have worked with the schedule and extremely tight site,” said Mickey Ankhelyi, AIA, Clark Pacific director of architecture. “I think our prefabrication approach and vertical integration were important factors in the selection process because we greatly minimized disruption and simplified communication on an already-congested construction site that has a limited laydown area.”
The multiyear Oyster Point project is now in its second phase, with hundreds of workers and heavy equipment on-site. This includes several cranes simultaneously erecting three large biotech lab buildings on a segment of the 50-acre property to be served by Parking Structure 2.
By contrast, Clark Pacific’s presence on the site where it is assembling the $80M PS2 is minimal, consisting of no more than 10 members of its field erection crew.
Ankhelyi said his firm’s small footprint allows general contractor Hathaway Dinwiddie to proceed relatively unimpeded with the construction of the three adjacent Phase 2 buildings totaling 865K SF while Clark Pacific assembles the approximately 2,000-stall PS2. Clark Pacific designed the long span open parking structure with minimal columns for easy access and egress. It is carved into a hillside with portions of four stories below grade to help mask the building’s height from motorists on nearby Oyster Point Boulevard.
“As the GC’s team began construction on the office buildings, they excavated and prepared a slightly larger than 2-acre work site for us,” he said. “And then we came in and started erecting the structure. It’s a very busy site, but prefabrication allows us to play well with the others in the same sandbox.”
With the parking structure’s segments manufactured off-site, Kilroy Realty can visit Clark Pacific’s plant in Woodland, California, to inspect and give input on the assembled building segments as work progresses. This way, any issues are addressed long before the parts depart from the manufacturing plant.
“The client was able to inspect the pieces at our yard before they were trucked to Oyster Point,” Ankhelyi said. “We did a mock-up of the structure at our plant and painted certain parts of it to allow them to understand how the finished building will look. None of that was done on the building site, which meant there was zero disruption to the other members of the construction team because everything was coordinated in advance.”
Ankhelyi said Kilroy also appreciates Clark Pacific’s vertical integration, which allows it to serve as the architect of record, parking consultant, manufacturer and general contractor on the parking structure, with all team members working in the client’s best interest. This is very similar to Kilroy’s own business model, which emphasizes a single point of contact approach, he said.
“At the end of the day, the client is really only dealing with one person for everything,” Ankhelyi said. “It streamlines the process, and the owner does not have to sign multiple contracts and work separately with each team member. We encompass different disciplines at Clark Pacific, but we share the same goals for the client and work together to achieve them.”
Clark Pacific has completed more than 180 parking projects on the West Coast. Ankhelyi said the company’s expertise and vertical integration allow it to anticipate and accommodate a client’s evolving priorities — even if it maintains no more than a modest presence on the construction site.
“We bring a lot of expertise in getting the most efficiency out of a job site and getting the best performance from the parking structure for whatever the client's needs may be,” he said.
This article was produced in collaboration between Clark Pacific and Studio B. Bisnow news staff was not involved in the production of this content.
Studio B is Bisnow’s in-house content and design studio. To learn more about how Studio B can help your team, reach out to [email protected].